Integrated management and optimization system for logistics facilities
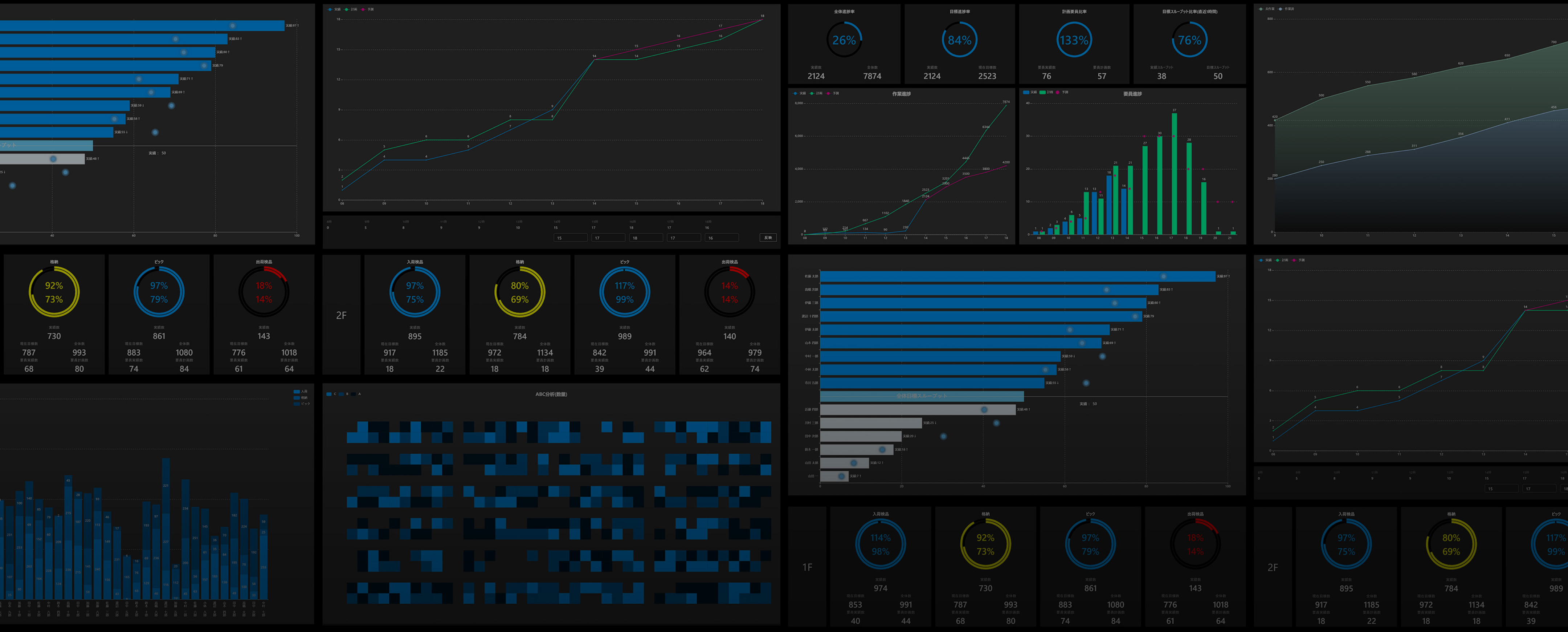
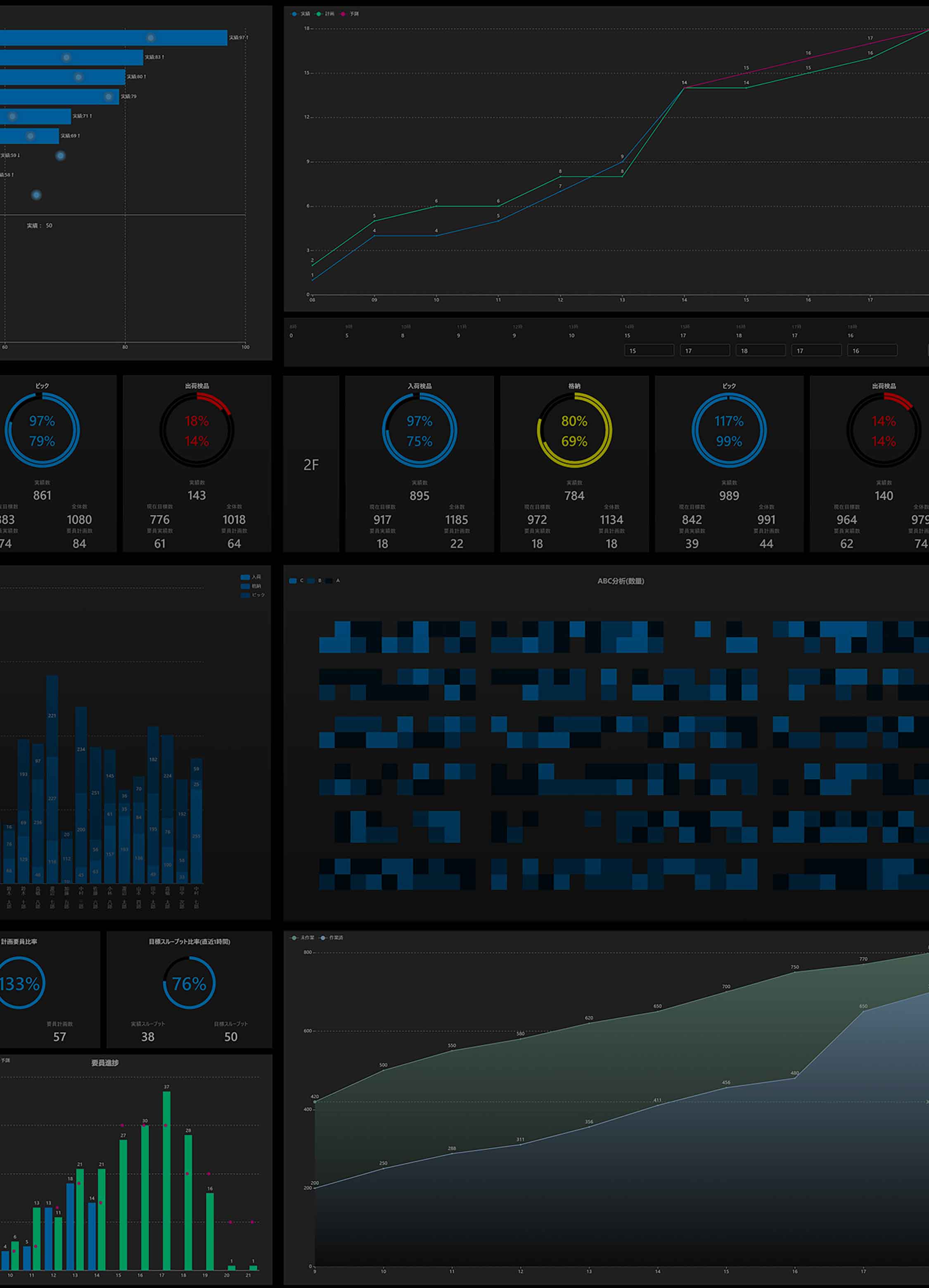
Optimization of Stoking Location, Picking Routes,
Delivery & Staff Allocation by GWES
Overview
GWES, the integrated management and optimization system for logistics facilities, helps to improve and optimize operation, stock location, delivery and staff allocation in logistics facilities.
-
Inventory Analyzer
-
Slotting Optimizer
-
Routing Optimizer
-
Delivery Optimizer
-
Loading Optimizer
-
Shift Creator
-
Resource Allocator
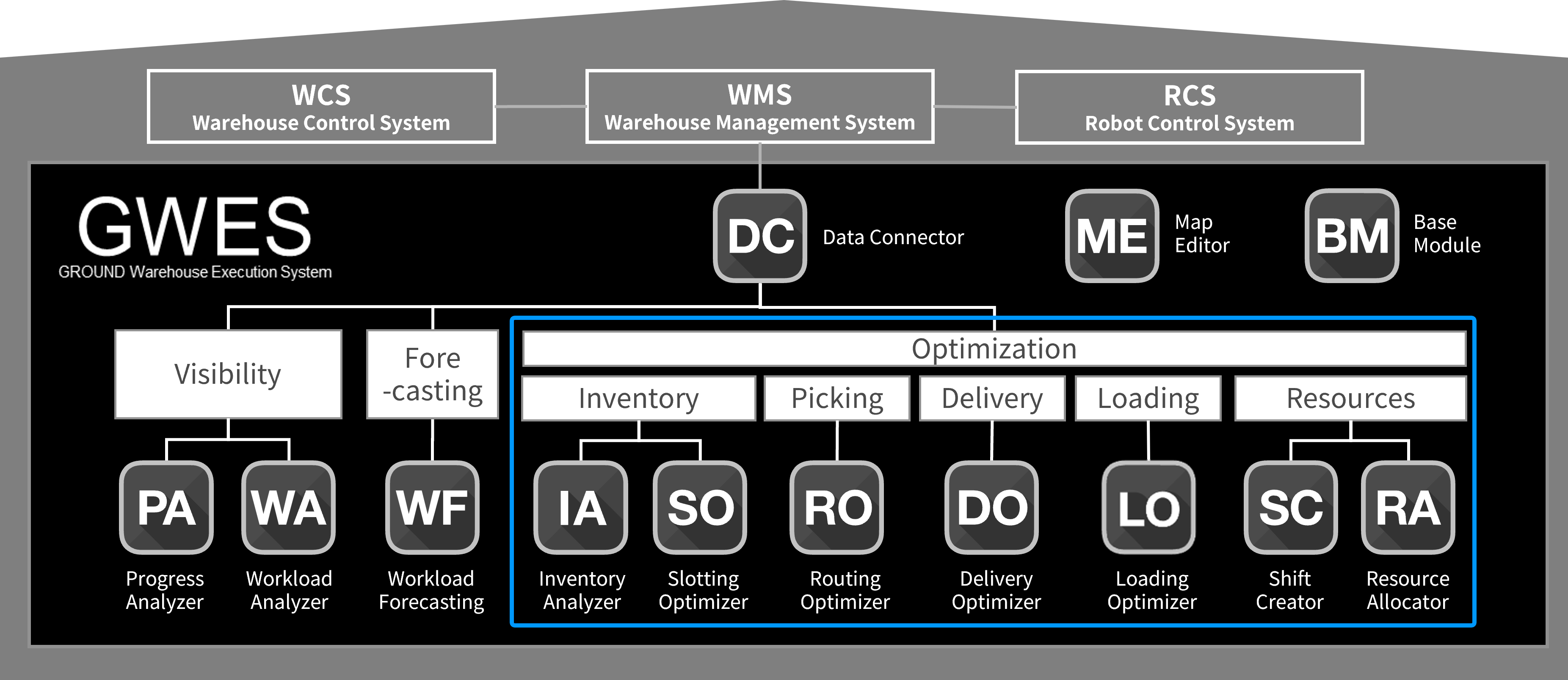
Features
Plans inventory allocations that improve work efficiency and storage efficiency
GWES plans inventory locations that improve the efficiency of picking process and of product storage by simultaneously analyzing a large number of parameters that is beyond the capability of manual processing.
Plans picking routes with the shortest travel distance and lowest costs
GWES automatically controls picking orders by analyzing information about orders that have been placed and consolidating orders for products that are stored close to each other, based on the load capacity of each equipment (forklifts, robots, roll box pallets, etc.). This reduces the distance traveled by workers in the picking process and helps improve overall throughput.
Delivery planning with the lowest costs
GWES generates delivery plans by selecting transport methods and vehicles to meet delivery constraints, such as delivery time and loading capacity, and to minimise costs, thereby reducing and optimizing delivery costs. In addition, the system can be linked to a warehouse management system (WMS) to manage the entire flow of goods from receipt to delivery.
Plans staff allocations based on work progress and forecast
GWES plans optimum staff allocation by watching work progress in real-time, for example by instructing them to move to another workshop for optimizing the site-level operational progress. In addition, optimum staff shift plans are generated in advance based on workload forecasts.